Image search results - "textile" |
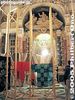
Textile exhibition 織物展The textiles were exhibited in the best rooms of the Palazzo Ducale, including the chapel shown here. Beautiful frescoes decorated the walls and ceilings. What a contrast it was between the Japanese kimono and religious motif.
織物は宮殿の一番豪華な多数の部屋に展示された。
|
|
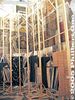
Textile exhibition 織物展The textiles included kimono, noren curtains, and stenciled works.
着物、のれんなど展示された。
|
|

Textile exhibition catalog: Avvolti Nel Mito 織物展図録The textiles exhibited are shown in this catalog called "Avvolti Nel Mito" (Wrapped in the Myth) published by Ideart. Language is Italian. Order from PhotoGuide Japan's iStore.
|
|
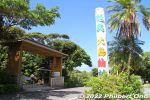
Oshima tsumugi is a local fabric woven from white silk and dyed. Oshima (Ooshima) Tsumugimura is a small textile factory where you can see how they weave and dye the tsumugi fabric. They also sell tsumugi fabrics as kimono, handkerchiefs, etc.
|
|
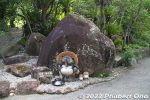
The factory is in a subtropical garden with tropical flowers and plants. Adult admission ¥500, open every day 9 a.m. to 5 p.m.Address: 1945 Akaogi Tatsugo Oshima, Kagoshima
Local buses stop at Oshima Tsumugimura bus stop. (From Amami Airport, 30 min. by bus.) http://www.tumugi.co.jp/
|
|
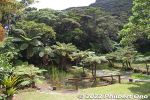
Tropical garden setting for this fabric factory. Oshima tsumugimura, Amami Oshima.
|
|

He is dyeing Oshima tsumugi silk fabric in mud.
|
|

He is dyeing Oshima tsumugi silk fabric in mud. The fabric color becomes black. Amami-Oshima island, Kagoshima.
|
|
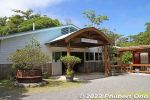
Oshima (Ooshima) Tsumugimura
|
|
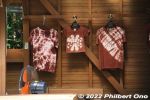
Tie-dyed (in mud) handkerchiefs. The fabric is also dyed with the sharinbai tree containing iron and tannin.
|
|
|
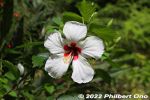
White hibiscus on Amami Oshima.
|
|
|
|
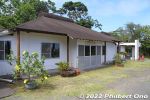
Oshima (Ooshima) Tsumugimura fabric factory.
|
|
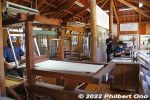
Inside the Oshima (Ooshima) Tsumugimura fabric factory. A few workers demonstrated the production of tsumugi silk fabric. This weaving step is called shimebata to make patterns on the silk.
|
|
|
|
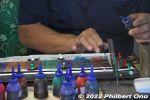
Fabric dyes.
|
|
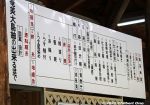
Oshima tsumugi fabric production steps.
|
|
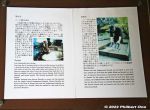
Explanation of the Oshima tsumugi dyeing process.
|
|
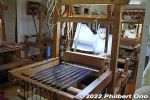
Loom
|
|

Loom to weave Oshima tsumugi.
|
|
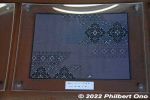
Sample Oshima tsumugi fabric with in the typical black color.
|
|
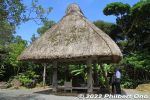
Takakura storehouse with a steep thatched roof. Amami's traditional structure for storing grains. Oshima tsumugimura, Amami Oshima, Kagoshima. 奄美の高倉
|
|
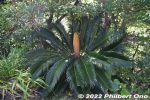
Sago palms with a cone. Oshima Tsumugimura, Amami Oshima, Kagoshima. ソテツ
|
|
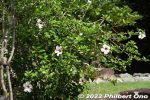
White hibiscus
|
|
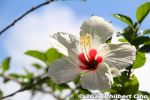
White hibiscus
|
|
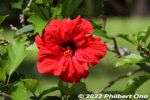
Red hibiscus and other flowers in the tsumugi factory's garden setting. Amami Oshima, Kagoshima
|
|

Sago palms, Amami Oshima, Kagoshima
|
|
|
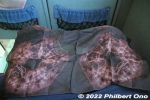
Oshima tsumugi handkerchief I bought for myself. Tie-dyed.
|
|
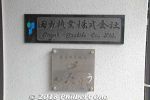
Visited a Tango chirimen company called Tayuh Textile Co., Ltd. (Tayuh Kigyo 田勇機業株式会社). http://www.tayuh.jp/
|
|
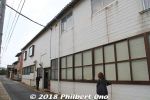
Tayuh Textile Co.'s chirimen textile factory in Kyotango.
|
|

Lobby of Tayuh Textile Co.
|
|
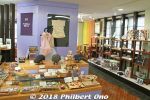
First we saw Tayuh Textile Co.'s gift shop and showroom.
|
|
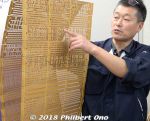
Tayuh Kigyo's third-generation company president Tamoi Hayato (田茂井 勇人) first explained about their chirimen manufacturing process.These looping punch cards called "mon-gami" (紋紙) program the Jacquard loom to weave the design on the fabric. The holes in the punch cards tell the loom which threads are to be raised or not during the weaving process. These punch cards can be made by computer now.
|
|
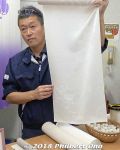
He showed us the finished product, a chirimen fabric with a woven design.
|
|

This is 3,000 silk cocoons. That's how much silk is needed to make silk fabric for one kimono. One cocoon has 1200–1500 meters of silk thread. Since Japan produces very little silk, most are imported from China and Brazil. The Tango region consumes about one-third of Japan's raw silk imports. We were told the quality of silk from China and Brazil is very good.
|
|
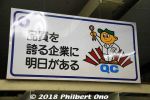
Tayuh Kigyo's company motto: "A company that boasts quality has a future."
|
|
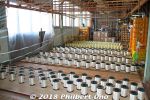
Tayuh Textile Co. makes almost everything, from the silk threads to the fabrics. We toured their impressive factory. These are spools of silk being made into threads.
|
|
|
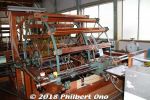
This is a thread twister to twist the horizontal silk threads (weft) 3,000 to 4,000 times. This is a key step and how chirimen gets its crimped surface. After being woven into the fabric, the highly twisted weft threads try to untwist, creating the crimping.
|
|
|
|
|
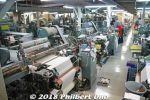
Tayuh Kigyo's factory has 60 mechanized looms (50 of them are Jacquard looms).
|
|
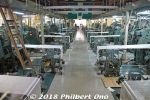
Very noisy and very fast-moving. One employee monitors several looms.
|
|
|
|
|

Fascinating to watch.
|
|
|
|
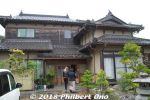
Tango chirimen silk fabric maker Tamiya Raden (民谷螺鈿).
|
|
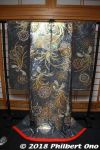
Tamiya Raden (民谷螺鈿) had this stunning silk kimono on display for us. "Raden" means inlay (using shell, ivory, etc.). Typically, we think of lacquerware, but they do it on fabrics. This kimono took 2.5 years to make and is worth more than a Lamborghini or Rolls Royce.
|
|
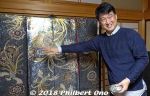
Company president Tamiya Kyoji answered our many questions about this amazing kimono. His father Tamiya Katsuichiro took two years to develop and invent a method to inlay shell pieces in fabrics and showed their first example on a kimono obi sash in 1977.
|
|
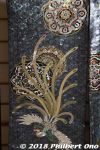
The kimono was woven with pearly shell pieces from five species of oysters. Might be hard to see which parts of the kimono are the shell inlay, but the shiny parts are not the shell pieces. Very glittery.
|
|
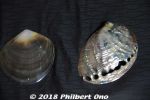
Pearly shells used in their fabrics.
|
|
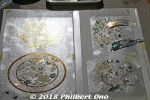
First they attach the thin shell/pearly layers on a design on washi paper.
|
|
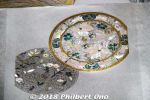
It's a painstaking, time-consuming process.
|
|
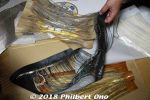
The completed design on washi paper is then sliced into "threads" that will be woven into the fabric.
|
|
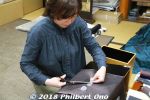
Working on an obi sash.
|
|
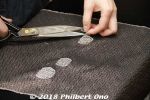
Working on an obi sash.
|
|
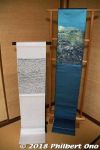
Tamiya Raden also makes kimono obi sashes.They also supply fabrics to world-famous luxury brands, but they can't brag about it because of a non-disclosure agreement.
|
|
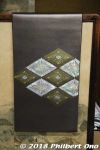
This is a replica of an obi sash that was selected and worn by Empress Michiko recently for her birthday.The company is especially proud of this, but can't publicly brag about it. (The empress does not know who made the obi. She just liked the design.)
http://tamiya-raden.jp/
|
|
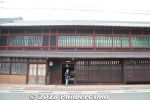
Another stop was a Tango chirimen wholesaler named Yoshimura Shouten (株式会社 吉村商店 峰山支店). Founded in 1830 and based in Kyoto city, this is their branch shop in in Mineyama, Kyotango.
|
|
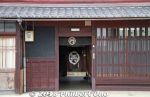
They are in this distinctive, traditional building rebuilt in 1930 after the big 1927 Tango earthquake.
|
|
|

Inside Yoshimura Shouten. They have a small office space on the right, meeting room on the left, a fireproof kura storehouse in the back, and lots of floor space for textile merchandise.
|
|
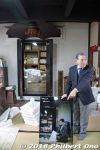
Mineyama Branch Manager Yoshioka Hitoshi shows a PR poster of Bando Tamasaburo V posing with a Tango chirimen fabric in front of the shop's kura storehouse near where Yoshioka is standing.Tamasaburo V is one of the most famous and popular kabuki actors in Japan and Living National Treasure. He loves Tango chirimen fabrics and kabuki costumes also use Tango chirimen.
|
|
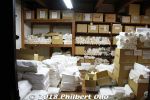
Inside their kura storehouse.
|
|
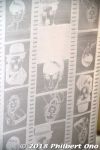
Yoshimura Shouten also creates its own designs like this "Hollywood chirimen" prototype with the the likeness of Audrey Hepburn, Charlie Chaplin, and Marilyn Monroe.
|
|
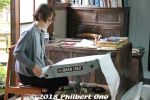
Chirimen fabric inspector uses a light box to carefully check for any defects and flaws in the material. Any defects in the material will reduce its value and the fabric (or kimono) will be sold for less.
|
|
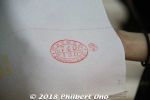
Seal of approval on chirimen fabric.
|
|
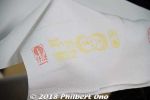
Seal of approval on chirimen fabric. Although Yoshimura Shouten is mainly a wholesaler, they also sell fabrics to individuals.http://yoshimura-shouten.jp/
|
|
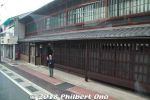
He even waved goodbye to us!
|
|
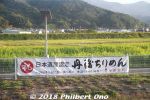
Banner commemmorating the 300th anniversary of Tango chirimen in 2018.
|
|
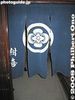
Konki Senshoku noren curtain. They've been in business in Konan for 200 years. One of three shops left in Shiga doing traditional indigo dyeing with natural (not synthetic) indigo dye. MAPTake a bus or taxi from Kosei or Mikumo Stations on the Kusatsu Line. Get off at Shimoda and walk 50 meters. Parking also available. Phone: 0748-75-0128, Address: Shimoda 1530, Konan-shi, Shiga
|
|

They grow their own indigo plants, dry the leaves in the sun, and extract the dye. They offer indigo dyeing lessons during which you can dye a cotton handkerchief for 1200 yen (T-shirts also). The kind lady first showed us samples of indigo fabrics.
|
|
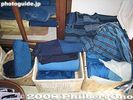
Indigo fabrics for sale. Around 2000 yen per meter. Indigo dyeing came to Shiga from Kyoto. Indigo dyeing is called "aizome" in Japanese. 藍染
|
|
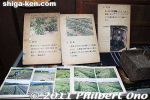
Pictures of their indigo plant farm in Konan.
|
|
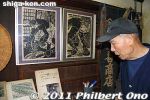
A student created a woodblock print of the indigo artisan dyeing threads.
|
|
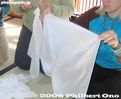
So here's the handkerchief (1200 yen). It's very thin cotton. 近江正藍染 <県知事指定・滋賀県伝統的工芸>
|
|

We fold up the handkerchief in whichever way, then tie strings/rubber bands around it. It is tie-dyeing.
|
|

Then we go to the indigo vats. They are heated with charcoal made with wood from trees on their hill. Each vat has a different indigo density.
|
|
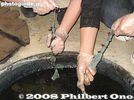
We started with a vat having a low density of indigo. We dip the handkerchief for 15 sec., wring it, then expose it to the air. The indigo dye is actually a murky brownish-yellow color, but turns blue when exposed to the air.
|
|
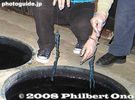
We dipped the handkerchief in multiple vats, each successive vat had a higher density of indigo. The more vats we dip the fabric in, the darker the color.
|
|
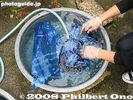
After the indigo dip, water washed the handkerchief.
|
|
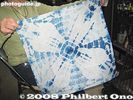
One result... All the designs are unique. We held the wet handkerchief in front of a kerosene heater and it dried quickly.
|
|
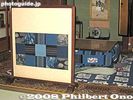
A room inside the shop had indigo fabrics everywhere. It takes years to learn the craft of indigo dyeing, including growing the plants. Like many other traditional crafts, this shop is uncertain who will take over and continue traditional indigo dyeing.
|
|
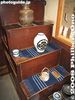
Indigo placemats on stairs. It's possible for the shop to handle up to 20 people to try indigo dyeing in their shop. Call 0748-75-0128. Address: Shimoda 1530, Konan-shi, Shiga
|
|
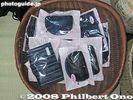
Pouches, etc., made of indigo fabric, for sale. Coming to this place really made me aware of how beautiful the indigo color is. Take a bus or taxi from Kosei or Mikumo Stations on the Kusatsu Line. Get off at Shimoda and walk 50 meters. Parking also avail
|
|
|
|
|
|