Image search results - "Otani" |
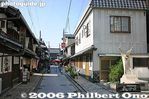
Nagahama's most famous temple belongs to the Jodo Shinshu sect, Otani school. Omotesando path to Daitsuji.
|
|
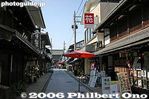
Omotesando is lined with shops.
|
|

Red paper umbrellas decorate the path.
|
|
|
|
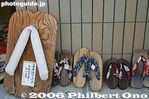
Sandal store
|
|
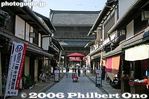
Getting closer to the Sanmon Gate
|
|
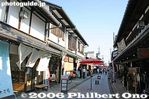
Omotesando as seen from Sanmon Gate.
|
|
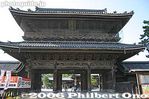
Daitsuji temple Sanmon Gate 山門
|
|
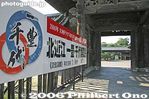
2006 NHK Taiga Drama "Komyo ga Tsuji" Exhibition banner and gate entrance.
|
|
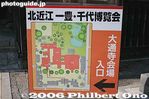
2006 NHK Taiga Drama "Komyo ga Tsuji" Exhibition mapThe temple was one of the venues for the special exhibition held for the NHK Taiga Drama "Komyo ga Tsuji" in 2006.
|
|
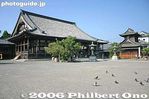
Daitsuji temple Hondo main hall and belfry
|
|
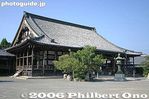
Daitsuji temple Hondo main hall 大通寺本堂 MAP
|
|
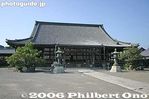
Daitsuji temple Hondo main hall 大通寺本堂
|
|
|
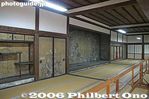
Large Hall 大広間. This is also one location where the film Idai Naru, Shurararabon (偉大なる、しゅららぼん The Great Shu Ra Ra Boom) was filmed. The sleepover scene.
|
|
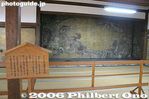
Large Hall 大広間
|
|
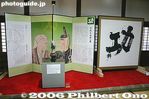
Komyo ga Tsuji exhibit showing Chiyo and Yamauchi Kazutoyo
|
|
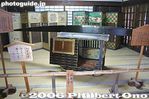
Entrance hall and palanquin 玄関
|
|
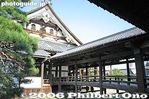
Corridor to main hall
|
|
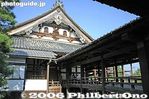
Corridor to main hall
|
|
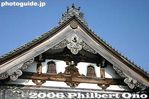
Main hall roof
|
|
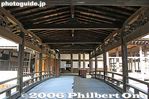
Corridor to main hall
|
|
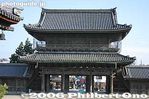
Sanmon Gate as seen from the Hondo main hall
|
|
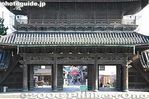
Sanmon Gate as seen from the Hondo main hall
|
|
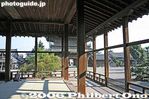
Main hall
|
|
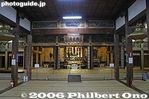
Hondo main hall altar 大通寺 本堂阿弥陀堂
|
|
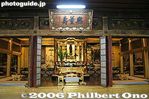
Hondo main hall altar, Important Cultural Property 大通寺 本堂阿弥陀堂
|
|
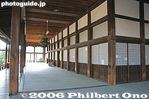
Main hall veranda
|
|
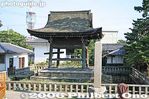
Belfry
|
|
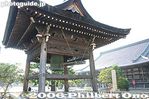
Belfry
|
|

Belfry surrounded by a pond
|
|

Tree
|
|

Straw blind
|
|
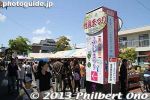
Path leading to the entrance of Takehana Betsuin temple.
|
|
|
|
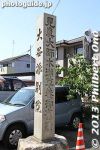
Takehana Betsuin temple belongs to the Jodo Shinshu Sect's Otani School (Higashi Hongwanji).
|
|
|
|
|
|
|
|
|
|
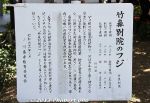
Takehana Betsuin temple's wisteria is over 300 years old.
|
|
|
|
|
|
|
|
|
|
|
|
|
|
|
|
|
|
|
|
|
|
|
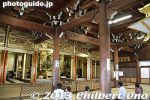
Inside Takehana Betsuin. Very impressive for a rural area.
|
|
|
|
|
|
|
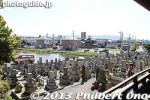
Cemetery next to the main hall.
|
|
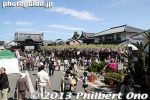
View from the Hondo main hall.
|
|
|
|
|
|
|
|
|
|
|
|
|
|
|
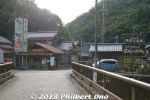
Kurotani is the name of the village (now part of Ayabe city) where they make Kurotani washi paper. This is the entrance to the small village in a valley.Kurotani Village started making washi about 800 years ago when 16 warriors of the Heike Clan defeated by the Minamoto Clan in Kyoto (Genpei War 1180–1185) fled and hid here to avoid capture. They and the local farmers made a living in summer by growing rice, but since there was nothing to do in winter, they thought of making washi paper. Washi can only be made in winter since it requires cold water.
|
|
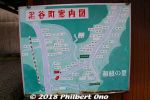
Kurotani Washi-no-Sato Japanese papermaking village in Ayabe, Kyoto.Once upon a time, there were a number of washi paper makers in northern Kyoto like Tango washi and Tanba washi, but now there's only one traditional maker that has survived called Kurotani washi. They work here in the small Kurotani Valley.
|
|
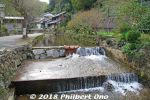
Kurotani village was blessed with this clean Kurotani River, essential for papermaking. Kurotani washi is quite famous now, even overseas.
|
|
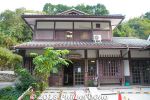
Kurotani village has this Kurotani Washi Kaikan gift shop (黒谷和紙会館). Kurotani is not touristy because it's not convenient to get here.
|
|
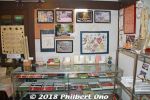
Inside Kurotani Washi Kaikan gift shop.
|
|
|
|

Kurotani washi mainly uses kozo or mitsumata mulberry plants as the raw material. This is our Kurotani washi guide showing us the kozo plants that can grow to three meters high.They are harvested in autumn by cutting the trunks or branches. They grow kozo mulberry near Ayabe Station. Kozo is called "kago" in Kurotani.
|
|
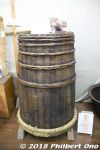
To make the paper fibers for washi, there are many laborious steps. After the kozo branches are cut in even lengths, they are stuffed in a barrel (koshiki) like this and placed over a boiling and steaming iron pot for three to four hours to soften the brown bark.
|
|
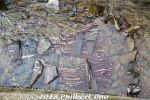
While the kozo branches are still hot, elderly ladies twist and strip off the brown bark (kuro-kawa 黒皮). The bark is dried, then soaked in river water like here.
|
|
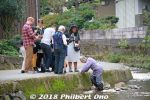
While soaking, the kozo bark is also kneaded by human feet to soften it. The water is cold, and it's a traditional job for the grandmas.
|
|
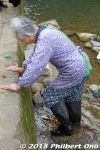
We just happened to come across her in the river kneadking the brown bark. How lucky we were.
|
|
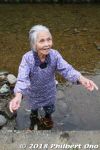
She's Horie Sayo, 86 years old, been doing it since her teens.
|
|
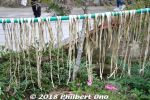
The brown kozo bark is shaved and scraped with a knife by hand to remove the brown bark skin and other blemishes. Then the becomes thin, white strips that are dried in the sun. (shiro-kawa 白皮)
|
|
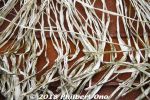
White kozo bark strips drying. These will then be mashed and beaten into fibrous globs. Preparing the kozo fibers from the bark is the most laborious and time-consuming part of washi making.
|
|
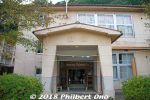
Also visited Kurotani Washi Kougei No Sato (Kurotani Washi Craft Village 黒谷和紙 工芸の里) a 20-min. car ride away.They were using an old elementary school.
|
|

They use the 1st floor for making paper, while the second floor are washi exhibition rooms.
|
|
|
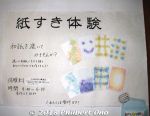
They offer washi papermaking lessons for ¥1,300 including admission.
|
|
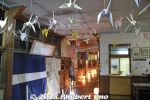
Entrance hall with origami cranes made of Kurotani washi. It really looks like an old school.
|
|
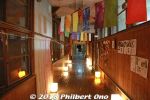
Corridor to rooms.
|
|
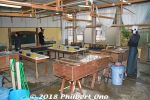
Washi papermaking room where we tried making Kurotani washi paper (postcards).
|
|
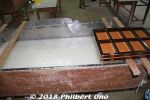
A large vat (sukifune) filled with washi fibers floating evenly in the water. The fibers are mixed in with a plant-based adhesive so they don't sink to the bottom and they also cling together to make the paper. A wooden mold (keta 桁) to make eight postcards on the right. Kurotani washi bills itself as Japan's strongest paper. In the 1920s, Kurotani washi was tested for strength and was declared the strongest washi in Japan. I was told Kurotani's kozo has longer fibers than other species so the paper is stronger.
|
|
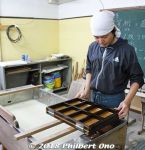
Our instructor first showed us how it was done. He used a mold to make eight washi postcards.
|
|
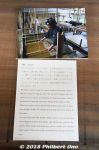
About sugeta.
|
|
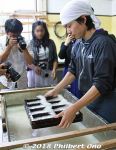
Dump the postcard mold into the vat and swish it left/right and forward/back evenly.
|
|
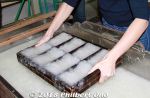
Takes three years to learn how to make washi paper with a mold. Ten years to become an expert. But we did it in a minute or two... Just dip the mold into the fibrous water, and swish it to the left/right and forward/back.
|
|
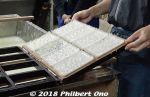
The postcards looked quite thick out of the mold, but they would get much thinner when dried.
|
|
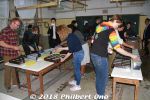
Afterward, we could decorate our postcards with colored ink/fibers.
|
|
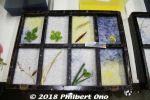
A few people even embedded leaves.
|
|
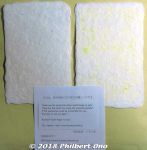
They later sent us our postcards. Mine came out okay.
|
|
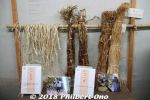
This shows how they typically hang and dry the white strips and bark strips.
|
|
|
|
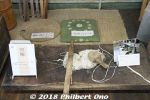
Later, it is mashed/beaten in a stone mortar.
|
|
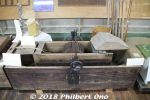
Then it goes through a mechanical beater for 10 min. to become a wet, fibrous mass. They also make and add a plant-based adhesive. Here's a good video (in Japanese) showing how they do it (the woman we saw in the river also appears in this video): https://youtu.be/-3ws9DlPVHo?t=425
|
|
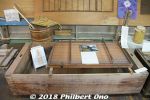
The vat and mold to make paper.
|
|
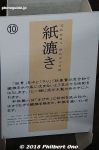
Kami-suki is what everyone can experience.
|
|
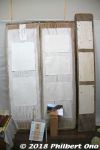
The washi shets are dried on wooden boards.
|
|
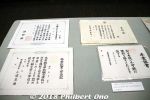
Local public schools have their kids make their diplomas with Kurotani washi.
|
|
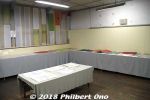
Second floor in former classrooms are exhibition rooms.
|
|
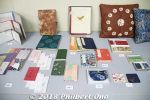
Kurotani washi has long fibers, making it very strong and durable. It has many uses such as umbrellas, shoji paper sliding doors, and packaging.
|
|
|
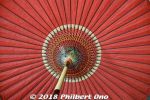
Kurotani washi can even be used for umbrellas.
|
|
|
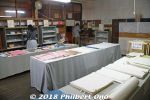
Gift shop.
|
|
|
|
|
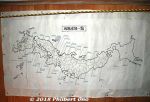
Places in Japan where washi is made.https://kurotaniwashi.kyoto
English: https://kurotaniwashi.kyoto/?page_id=450
|
|
|
|